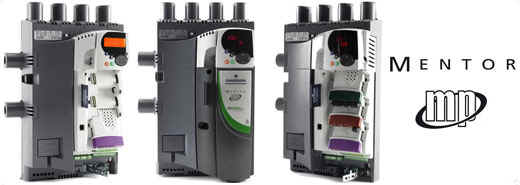
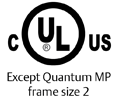
Modern, cost effective DC drive with excellent
system integration flexibility
25 A – 7,400 A (5 hp – 6,500 hp)
24 V - 480 V | 575 V | 690 V
Control Techniques’ Mentor MP brings DC
drive technology up to date, enabling existing and new
DC motors to provide economic and productive service.
DC drive technology remains cost
effective, efficient and is relatively simple to
implement.
208-460 / 575 Volts
3Ø Flexible DC drive

Overview
Mentor MP is Control Techniques' 5th generation DC drive and
integrates the control platform from the worlds leading intelligent AC
drive, Unidrive SP. This makes Mentor MP the most advanced DC drive
available, giving optimum performance and flexible system interfacing
capability.
Upgrading your control system
There are large numbers of DC motors in service throughout
the world in various applications, the majority of which are easily capable
of providing continued service. Upgrading your drive allows you to maximize
the motor performance, enhance system reliability and interface digitally
with modern control equipment using Ethernet and Fieldbus networks. Downtime
is minimized as only the drive needs to be replaced.
Driving forward with DC technology
DC drive technology remains cost effective, efficient and is
relatively simple to implement. For new solutions DC provides many
advantages, especially for regenerative and high power applications.
Applications
Our extensive expertise across a wide range of industries
mean that we are the ideal partner for DC solutions.
Typical applications for Mentor MP include: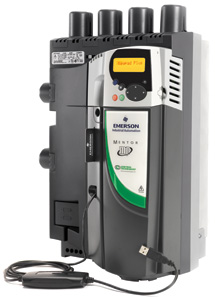
Benefits
-
Unparalleled flexibility through the integration of
Control Techniques AC control platform on a DC drive
-
Maximum reliability achieved through unique protection
system against poor quality industrial power supplies and
lightning strikes
-
Protected control circuits, galvanically isolated from the
high voltage circuitry using unique patented (pending) technology
-
System integration with modern communication networks
including, Ethernet, EtherCAT and DeviceNet
-
Easy replacement for Mentor II with the same dimensions,
power connection locations and easy to use software conversion tools
-
6, 12 and 24 pulse systems for reduced harmonics
-
RoHS compliant
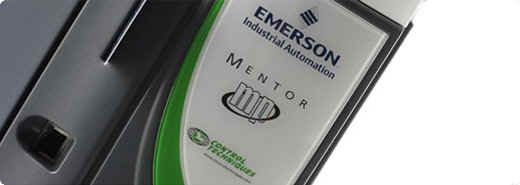
Mentor MP, the ultimate drive solution
-
Models available for two or four quadrant (regenerative)
operation
-
Modular serial and parallel connection for higher power
motor operation
-
12/24 pulse operation to minimize harmonics
-
Integrated drive and motor protection for:
-
Over current
-
Over Voltage
-
Over temperature
-
Phase loss
-
SCR (Thyristor) junction temperature
-
Feedback loss
-
Field loss
-
Armature open circuit
-
3 Universal option module slots, allowing Mentor MP to
benefit from the solutions developed for Control Techniques market leading
AC drive technology. Each option slot can accept any combination of the
following modules:
-
High performance PLC and motion control
-
Ethernet and Fieldbus communications
-
Connectivity to additional feedback devices
-
Additional I/O
-
Galvanically isolated control
-
Open loop control using estimated speed based on armature
voltage and field flux
-
Closed loop control using
-
Tach-generator feedback for connection to traditional DC
motors
-
Incremental encoder feedback for higher accuracy and
position control
-
Optional SinCos, SSI, Hiperface and EnDAT connectivity for
high performance applications
Field Control
Internal field controller with intelligent field weakening
(90% of applications no additional external controller is required)
-
Frame Size 1 to 8A
-
Frame Size 2A and 2B to 10A
-
Frame Size 2C and 2D to 20A
-
Flux control for enhanced open loop performance
Optional FXMP25 external field controller for field currents
up to 25A
-
Digital link for field control from Mentor MP or Mentor II
-
Standalone digital control mode for simple application
-
Flux control for enhanced open loop performance
-
Intelligent field weakening
-
Field forcing - for high dynamic machine reversal
-
Field reversal - low dynamic machine reversing using two
quadrant main stack
Mentor MP field control mode for fields requiring greater
than 25A
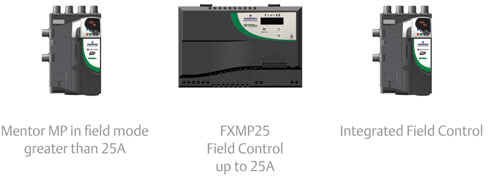
FXMP25 available 2010
Mentor MP, the ultimate drive solution
-
Models available for two or four quadrant (regenerative)
operation
-
Modular serial and parallel connection for higher power
motor operation
-
12/24 pulse operation to minimize harmonics
-
Integrated drive and motor protection for:
-
Over current
-
Over Voltage
-
Over temperature
-
Phase loss
-
SCR (Thyristor) junction temperature
-
Feedback loss
-
Field loss
-
Armature open circuit
-
3 Universal option module slots, allowing Mentor MP to
benefit from the solutions developed for Control Techniques market leading
AC drive technology. Each option slot can accept any combination of the
following modules:
-
High performance PLC and motion control
-
Ethernet and Fieldbus communications
-
Connectivity to additional feedback devices
-
Additional I/O
-
Galvanically isolated control
-
Open loop control using estimated speed based on armature
voltage and field flux
-
Closed loop control using
-
Tach-generator feedback for connection to traditional DC
motors
-
Incremental encoder feedback for higher accuracy and
position control
-
Optional SinCos, SSI, Hiperface and EnDAT connectivity for
high performance applications
Options
Keypads
A wide range of option modules are available to allow you to
customize Unidrive SP for your application.
-
Keypads
-
Programmable Control
-
Field Regulator
-
Communications
-
Feedback
-
I/O
-
Remote I/O
MP Keypad
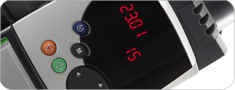
LCD Keypad with MP firmware

SM-Keypad
High visibility LED keypad

Programmable Control
SM-Applications Plus
High performance programmable automation and motion
controller with high speed I/O, CTNet and CTSync drive-to-drive
communications. Programmed using SyPTPro development environment.

SM-Applications Lite V2
High Performance programmable automation controller for
stand alone applications. Programmed using SyPTPro or SyPTLite
development environments.
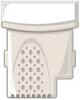
SM-Register - High Speed Motion & Registration
Control
SM-Register is designed to provide a
flexible, high performance solution for programmable motion requiring high
speed registration features. It is ideal for applications such as printing,
packaging and cutting machinery.
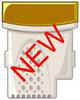
Field Regulator
FXMP25
Optional FXMP25 external field controller for field currents
up to 25A (available 2010)
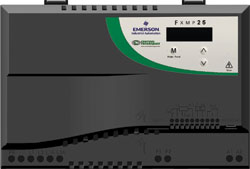
FXMP25 available 2010
Communications
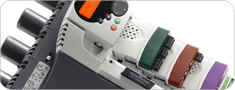
SM-Ethernet
Ethernet option module supporting Ethernet/IP
and Modbus with built in web server.
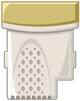
SM-Profibus
Profibus DP follower option module
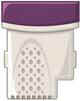
SM-EtherCAT
EtherCAT follower option module for high performance
applications
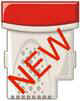
SM-DeviceNET
DeviceNET option module
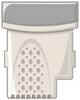
SM-CANopen
CANopen interface supporting various profiles including
several drive profiles
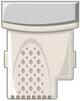
SM-Interbus
Interbus interface option module

Feedback
SM-Universal Encoder Plus
Combined encoder input and output interface supporting
Incremental, SinCos, Hiperface, EnDAT and SSI encoders

SM-Encoder Output Plus
Incremental encoder output option module to enable
connection with external motion controllers
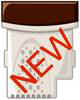
SM-Encoder Plus
Incremental encoder input option module
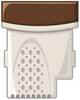
I/O
SM-I/O 32
Extended digital I/O adding 32 bi-directional I/O points
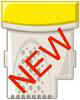
SM-I/O Plus
Extended I/O interface to increase the number of I/O points
on a drive
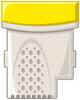
SM-I/O Lite
Extended I/O interface with reduced functionality
SM-I/O Timer
Extended I/O option module with real time clock
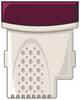
SM-I/O PELV (Protective Extra Low Voltage)
Namur NE37 and IEC 61800-5-1 standard I/O interface with
high speed I/O
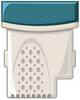
SM-I/O 120
120 volt I/O option module

Remote I/O
CTNet I/O
Flexible I/O system for remote connectivity using Control
Techniques' CTNet Drive-to-drive network

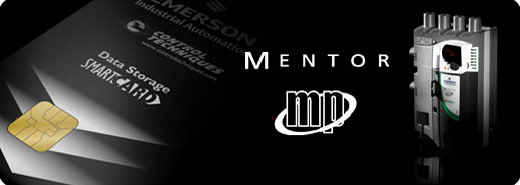
Software
Control Techniques' software suite makes it easy to access
the complete feature set of our drives. These tools provide quick
setup of the drive, optimize tuning, configuration back-up, programmable
control and communications link set up.
-
CTSoft - Drive configuration
-
CTScope - Software oscilloscope
-
SyPTLite - Ladder program editor
-
SyPTPro - Full automation system programming tool
-
CTOPCServer - OPC compliant server for interfacing with
Control Techniques' drives
The Software tools communicate using Ethernet, CTNet,
Serial or USB connections. Ethernet allows the software tools to easily
use the internet infrastructure allowing Control Techniques drives to be
accessed remotely, from virtually anywhere around the world.
CTSoft
CTSoft is a configuration tool for commissioning, optimizing
and monitoring Control Techniques drives. It allows you to:
-
Easily configure the drive using wizards
-
Read, save and load drive configuration settings
-
Manage the drive's smartcard data
-
Monitor drive parameters and status
-
Visualize and modify the configuration with live animated
diagrams
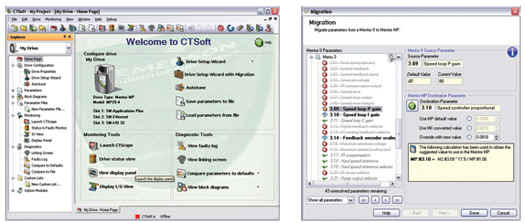
CTSoft is free of charge and can be obtained by clicking the
download tab on this page.
CTScope
CTScope is a full featured software oscilloscope for viewing and
analyzing changing values within the drive. The time base can be set
to give high speed capture for tuning or intermittent capture for longer
term trends. The interface is based on a traditional oscilloscope,
making it familiar to engineers across the globe.
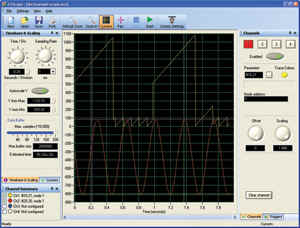
CTScope is free of charge and can be obtained by clicking the download
tab on this page.
SyPTLite
SyPTLite is an easy to use ladder logic program editor, suitable for
simple drive applications. SyPTLite is ideal for controlling basic logic and
sequencing onboard PLC and with SM-Applications Lite V2 option module.
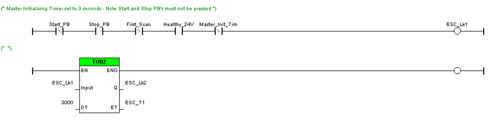
SyPTLite is free of charge and can be obtained by clicking the
download tab on this page.
SyPTPro
SyPTPro is a full featured automation development environment that can be
used for creating solutions to single or multiple drive
applications. The programming environment fully supports three industry
standard programming languages: Function Block, Ladder and Structured Text.
Motion is configured using PLCopen function blocks that support a master and
slave axis configuration.
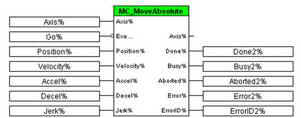
SyPTPro is also used to configure CTNet, a high speed drive-to-drive
network that links together multiple drives, SCADA, operator panels and
I/O to form an intelligent networked system.

CTOPCServer
CTOPCServe is an OPC compliant server that allows PCs to communicate with
Control Techniques' drives. The server supports communication using
Ethernet, CTNet, Serial RS485 and USB. OPC is a standard interface on
SCADA packages and is widely supported within Microsoft products. The
server is supplied free of charge and can be obtained by clicking the
download tab on this page.
Software
Overview
Control Techniques' software tools make it easier to access
the drive’s full feature set. Our software allows you to optimize the
drive tuning, back-up the configuration, configure the on-board automation
and motion controller and setup the drive-to-drive communications
links.
Commissioning software packages:
-
CTSoft - Drive parameter configuration and index motion
editor
-
MentorSoft - Drive parameter configuration &
index motion editor
- Mentor & Quantum series
-
SXSoft - Drive parameter configuration and index motion
editor for Commander SX series
-
CTScope - Real-time software oscilloscope
Programming software packages:
-
PowerTools Pro - Complete programming for
servo applications
-
SyPTPro - Drive automation and motion programming
environment
-
SyPTLite - Ladder program editor for simple PLC control
-
MotionPerfect2 - Programming Software for our
MC Series (Multi-Axis Motion Controllers)
Drive Selection software packages:
Connectivity software packages:
The software packages connect using Ethernet, CTNet,
Serial or USB connections. Ethernet communications allow the drives to be
accessed remotely, anywhere in the world.

|