CT Energy Savings
Control Techniques' energy optimization software helps
you analyze energy usage for different applications and calculate cost
savings using variable speed drives.
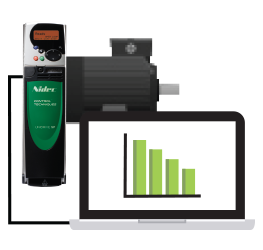
Features of the CT Energy Savings software:
-
Estimation of energy usage using variable frequency
drives for fan and pump applications
-
Comparison of energy consumption between variable
frequency drives and conventional control methods
-
Display of energy cost, savings and payback data
-
Graphical representation of flow versus cost, hours
and time
-
Customized client report facility including view,
print, e-mail and file export functions
-
Built in engineering calculator for horse power,
torque, AC motors, Ohm's Law and AC power circuit
calculations
-
Specifications
CT Energy Savings Estimator system
requirements:
-
Personal Computer or Notebook (Pentium or
faster) running Windows 2000, XP, 2003 Server
-
Memory: 256 MB RAM for Windows 2000/XP
-
Monitor: VGA or higher with a minimum
resolution of 800x600 (256 colors)
-
Hard Disk: 15MB Available Disk Space
-
Windows-compatible ink jet or laser printer
for printing of reports (optional)
-
Application Programming Interface (MAPI) to
e-mail report (optional)
CT Harmonics Estimator Software
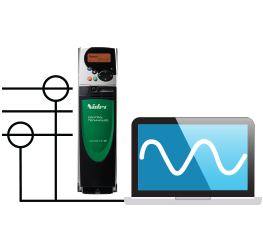
This supply-side harmonics estimator helps you to
economically meet the standards for specific application requirements.
Features of CT Harmonics Estimator Software:
-
Complete harmonic analysis for a system of drives
-
Facility to analyze drives configured for 12, 18 or
24 pulse drives
-
Comparison of results with limits required by IEEE
519 AND iec 61000-2
-
Display of results in tabular form or as a histogram
-
Specifications
Control Techniques Harmonics Estimator
system requirements:
-
Pentium III 500MHz or better recommended
-
Windows Vista, 2000 or XP. Windows
95/98/98SE/Me/NT4 are not supported
-
Memory: 128 MB RAM
-
Monitor: VGA or higher with a minimum
resolution of 800x600 (256 colors) 1024x768 is recommended
-
Adobe Acrobat 5.05 or later
-
Microsoft .NET Framework 2.0
-
Internet Explorer plus internet access. If
.NET Framework 2.0 is not installed with the operating
system (affects Windows 2000 only) an attempt to download
the requisite files will be made from Microsoft
-
Windows-compatible ink jet or laser printer
for printing of reports (optional)
CT Energy Savings
Control Techniques' energy
optimization software helps you analyze
energy usage for different applications and
calculate cost savings using
variable
speed drives.
Features of the CT Energy
Savings software:
-
Estimation of energy
usage using
variable frequency drives for fan and
pump applications
-
Comparison of energy
consumption between variable frequency
drives and conventional control methods
-
Display of energy cost,
savings and payback data
-
Graphical representation
of flow versus cost, hours and time
-
Customized client report
facility including view, print, e-mail
and file export functions
-
Built in engineering
calculator for horse power, torque,
AC
motors, Ohm's Law and AC
power circuit calculations
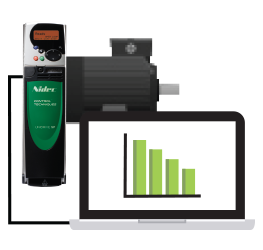
-
Specifications
CT Energy
Savings Estimator system
requirements:
-
Personal
Computer or Notebook (Pentium or
faster) running Windows 2000,
XP, 2003 Server
-
Memory: 256 MB
RAM for Windows 2000/XP
-
Monitor: VGA or
higher with a minimum resolution
of 800x600 (256 colors)
-
Hard Disk: 15MB
Available Disk Space
-
Windows-compatible ink jet or
laser printer for printing of
reports (optional)
-
Application
Programming Interface (MAPI) to
e-mail report (optional)
CT Harmonics Estimator Software
This supply-side harmonics estimator
helps you to economically meet the standards for
specific application requirements.
Features of CT Harmonics Estimator
Software:
-
Complete harmonic analysis for a
system of drives
-
Facility to analyze drives
configured for 12, 18 or 24 pulse drives
-
Comparison of results with limits
required by IEEE 519 AND iec 61000-2
-
Display of results in tabular form
or as a histogram
-
Specifications
Control Techniques
Harmonics Estimator system requirements:
-
Pentium III 500MHz or better
recommended
-
Windows Vista, 2000 or XP.
Windows 95/98/98SE/Me/NT4 are not supported
-
Memory: 128 MB RAM
-
Monitor: VGA or higher with
a minimum resolution of 800x600 (256 colors)
1024x768 is recommended
-
Adobe Acrobat 5.05 or later
-
Microsoft .NET Framework 2.0
-
Internet Explorer plus
internet access. If .NET Framework 2.0 is
not installed with the operating system
(affects Windows 2000 only) an attempt to
download the requisite files will be made
from Microsoft
-
Windows-compatible ink jet
or laser printer for printing of reports
(optional)
Programming Software
Digistart Soft
Control Techniques’ Digistart Soft is
an easy to use, fully functional PC tool for controlling, monitoring,
and programming the compact Digistart D2 and the
intelligent Digistart D3 soft starters.
Digistart Soft provides the following
functionality:
-
Operation of soft starter networks containing up to
31 individual soft starters.
-
Operational control (Start, Stop, Reset, Quick Stop)
-
Starter status monitoring (Ready, Starting, Running,
Stopping, Tripped)
-
Upload parameter settings/Download parameter
settings.
-
Save soft starter network groups to file.
Features
Digistart Soft can manage soft starters individually or
as a network group. Digistart Soft can manage multiple soft starter
networks. Some functions may not be available with some soft starter
models.
Starter Data panel:
-
The Starter Data Panel provides information about
the connected soft starter.
-
Depending on the starter type, model information may
not be available.
-
The digital display shows real-time performance
information, such as motor current (A) or motor temperature.
-
Specifications
System Requirements
The minimum system requirements for
Digistart Soft are:
-
40 MHz processor (1 GHz or higher
recommended)
-
96 MB RAM (256 MB recommended)
-
12 MB free space
-
1024 x 768 display, 32 bit
-
Microsoft Windows 98 SE, ME, NT, 2000, 2003,
XP or Vista (64-bit device drivers will be required if
running on a 64-bit operating system).
-
Microsoft .net Framework 2.0 (this will be
downloaded from Microsoft during installation if it is not
already loaded); this requires an additional 500 MB disk
space)
Machine Control Studio Software
Control Techniques' Machine Control
Studio provides a flexible and intuitive
environment for programming
Unidrive M’s
new automation and motion control features.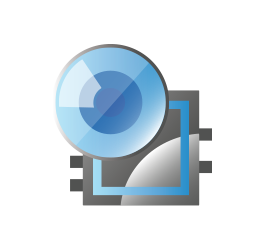
The new software offers programming
for:
-
Unidrive M400, M600 and M700’s onboard
PLC
-
High performance MCi200 and
MCi210 Machine Control module modules
-
Ethernet network data configurations
Machine Control Studio is
the leading open software for programmable machine control.
The programming environment is fully IEC 61131-3 compliant,
meaning that it is familiar and therefore fast and easy to
use for control engineers around the world. Control Studio
is the leading open software for programmable machine
control. The programming environment is fully IEC 61131-3
compliant, meaning that it is familiar and therefore fast
and easy to use for control engineers around the world.
The following IEC 61131-3
programming languages are supported:
Also supported:
Intuitive IntelliSense
functionality helps to write consistent and robust
programming, speeding up software development. Programmers
have access to a vibrant open-source community for function
blocks.
Control Techniques also
provides support for customers’ own function block
libraries, with on-line monitoring of program variables with
user defined watch windows and help for on-line change of
program, in line with current PLC practice.
-
Specifications
System requirements
Required:
-
Operating systems: Windows XP,
Windows Vista and Windows 7
-
RAM: 512MB
-
Hard disk: 500MB
-
Processor: Pentium V, Centrino >
1,8 GHz, Pentium M > 1,0GHz
Recommended:
-
Operating systems: Windows XP
-
RAM: 1024MB
-
Hard disk: 1GB
-
Processor: Pentium V, Centrino >
3,0 GHz, Pentium M > 1,5GHz
Engineering Control Studio
is only tested under the following operating
systems:
-
Windows XP
-
Windows Vista (32 bit)
-
Windows 7 (32/64 bit)
For communicating with a
Unidrive M drive you will also require a serial
port on your computer (or a USB to RS232 converter),
a RS232 to RJ45 communications lead or for Ethernet
based communications a RJ45 Ethernet lead. The RS232
lead is available from Control Techniques.
You must have administrator rights
under Windows XP/Vista/Windows 7 in order to install
this software.
PowerTools Pro Servo Software
Advanced motion control programming for
Epsilon EP, FM-3E and FM-4E modules, and for Control Techniques'
Unidrive SP and
Digitax ST-Z drives (with the
SM-EZMotion Option Module).
Our complimentary PowerTools Pro software
enables you to fully realize the power of our SM-EZMotion, FM
modules, Epsilon EP servo systems. A familiar Microsoft® Windows™
interface provides operators and machine builders with the tools needed
to access everything they need for complete servo control —PLS, Queuing,
Analog-In, User Variables, High-Speed Capture, Electronic Gearing, and
more.
Setup and Programming is made easy with our free, drag
and drop, PowerTools Pro software which programs the entire “Motion Made
Easy”™ product family. PowerTools Pro is free of charge and can be
obtained from our download section.
Developing motion applications with PowerTools Pro is a
simple “five step, top-down process”. The five steps are displayed
within an explorer bar that allows easy navigation. Each step is
configured using simple check boxes, drop down selections and drag and
drop functionality.
Five steps to develop motion applications with
PowerTools Pro:
-
Hardware Configuration
-
Drive Setup
-
I/O Setup
-
Motion
-
Programs
PowerTools Pro is a “BASIC”-like
programming language enabling users to develop more complex applications
and sequencing with functions being selected by dragging and dropping
onto the work area.
Control Techniques' programming software enables you to
fully realize the power of our entire servo product line including;
Digitax ST, Epsilon EP, MDS and Unidrive SP. A familiar Microsoft®Windows™
interface provides operators and machine builders with the tools needed
to access everything they need for complete servo control — Motion
Profile Setup, User Units, Motor Auto-tune, Electronic Gearing, Network
Configuration, and many other advanced features.
Note: New advanced PowerTool Pro 5.0
features are not supported on FM3 & FM4 modules, but are supported on
our FM3E, FM4E modules and all other
servo drive
products.
Assignments – Use our "Virtual Wiring"
to create programs right out of the box, without writing a single "line
of code." For example; the assignment screen simply drag-and-drop the
desired machine function onto the digital inputs and outputs.
Indexes – Setting up indexes is easily
accomplished by filling in the screen’s blanks to create an index
profile. Select from Incremental, Absolute, Registration, or Rotary Plus
and Minus types. With our Position Tracker synchronization can be easily
achieved by simply adjusting the time bar. Choose the time base of the
index by selecting either real time or synchronized to a master.
Network – Whatever Fieldbus you are using, setting up
network communications is quick and easy. Fill-in-the-blank,
drag-and-drop procedures are used to get your drives communicating.
PowerTools Pro diagnostics couldn’t be more intuitive, allowing
real-time monitoring of the actual data being sent and received.
Camming – Cam data is easily entered
within PowerTools Pro, and the Cam graphing tool is second to none, with
multiple interpolation types available.
SyPTLite
SYPTLite is a ladder diagram editor that allows users to
develop simple programs for Control Techniques drives
and option modules.
The software is designed to be easy to use to make
program development as fast as possible.
SyPTLite programs are developed using
ladder logic, a graphical language widely used to program PLCs. SYPTLite
allows a user to "draw" a ladder diagram representing a program.
SyPTLite includes basic ladder logic symbols and many advanced functions
such as:
-
Arithmetic blocks
-
Comparison blocks
-
Timers Counters
-
Multiplexers
-
Latches
-
Bit manipulation
-
Smartcard access blocks
Typical applications include:
-
Specifications
SyPTLite can be used for programming for
the following drives:
-
Commander SK fitted with a LogicStick
-
Unidrive SP standard onboard
-
Digitax ST standard onboard
-
Mentor MP standard onboard
-
SM-Applications Lite V2 option module for
faster program execution and additional memory
SyPTPro
At the heart of Control Techniques intelligent drives
are their automation capabilities, this is achieved through click-in
drive option modules that provide high speed access to the drives
real-time parameter set. These option modules are configured though
SyPTPro, a professional drive-programming toolkit for high performance
machinery applications.
The software provides a full featured programming
environment for PLC and motion control onboard Control Techniques AC, DC
and servo drives, together with full network configuration for systems
combining drives, I/O and operator interfaces.
SyPTPro Software Note: Support has been added for
the SI-Applications Plus module (Unidrive M700). This will upgrade
requires a previously registered version of SyPTPro (v2.0.5 onwards).
If you require an upgrade from an older version of the
product contact our Customer Service team.
-
Features
SyPTPro is designed for use with Control
Techniques SM-Applications range of option modules
onboard Unidrive SP, Affinity, Digitax ST or Mentor MP
drives, the software provides a programming environment for high
performance motion and PLC functionality.
Each applications option module incorporates
it’s own dedicated high-performance microprocessor to ensure
high speed program execution.
Drive-to-drive networking
Linking multiple drives, I/O, operator
interfaces and PC based devices together enables Control
Techniques to build high performance automation systems. SYPTPro
is used to easily and quickly configure CTNet, a deterministic
industrial network that is robust and tolerant to noise and
interference. A single CTNet network may connect to up to 255
nodes, with up to 20 nodes in a segment and segments connected
together using hubs, allowing large or small drive systems to be
managed and extended.
Programming environment
The SyPTPro multitasking environment allows you
to configure both event and time based tasks that are
synchronized to the drives internal control loops. This allows
you to reduce delays which enhances performance and prioritize
your software according to the speed of execution and
determinism required. SyPTPro supports three industry standard
programming languages giving you the flexibility to use the most
appropriate language for each part of your application, helping
you to write software that is structured and re-usable. The
three languages are Function Block, Ladder and DPL (Drive
Programming Language) structured text.
Motion and position control
SyPTPro can be used to configure high
performance motion control systems using Control Techniques APC
(Advanced Position Controller) that provides highly flexible
motion functionality including complex positioning, cams and
electronic gearing.
Program development, diagnostics and
monitoring
To reduce the time required to develop new
programs, program Stepping and Breakpoints can be configured
allowing the SyPTPro program to be paused or stepped to de-bug
software. While a program is being executed, SyPTPro shows the
real-time values within Function Block, Ladder and DPL
structured text programs. In addition watch windows can be
created that show the real-time status from multiple variables
across different nodes across a CTNet network.
Protect your intellectual property
SyPTPro gives you the option to protect your
knowledge by choosing to download only the compiled binary file,
and not the embedded source file to the application module. This
binary file is not up-loadable and so ensures that your
intellectual property remains yours. User Defined Function
Blocks allows you to develop your own function block library and
package them into secure binary files. The library may then be
distributed and used in other programs. The binary file does not
contain the original source code, and so your intellectual
property remains protected.
-
Specifications
SyPTPro is compatible with the
following operating systems:
SyPTPro can be used with the following
Control Techniques drives:
DRIVE |
OPTION MODULE |
CTNet NETWORKING |
Unidrive SP |
SM-Applications Lite V2 |
No |
Unidrive SP |
SM-Applications Plus |
Yes |
Digitax ST Indexer |
On-board |
No |
Digitax ST Plus |
On-Board |
Yes |
Mentor MP |
SM-Applications Lite V2 |
No |
Mentor MP |
SM-Applications Plus |
Yes |
Affinity |
SM-Applications Lite V2 |
No |
Affinity |
SM-Applications Plus |
Yes |
The amount of memory available for user
application is:
MEMORY TYPE |
MEMORY AVAILABLE |
Flash size available (for user
program) |
384kb |
RAM size available (for user
variables) |
80kb |
Motion Perfect2
MotionPerfect2 is software for motion
control programming of our MC series multi-axis controllers. The MC
Series is programmed with a powerful and fast multi-tasking BASIC
language. Programs are stored on the MC as full programs and use an
innovative on-the-fly compiling technique.
The on-the-fly compiling technique provides all the
performance benefits of compiled machine code while allowing for upload
and full program access, without the need for source code download.
MotionPerfect2 software is free of charge and can be obtained from our
web site.
-
Features
-
Programming software for MC series
-
Project manager loads/saves programs
-
Multi-program screen editor
-
Multiple terminal windows
-
4-Channel oscilloscope to monitor parameters
& I/O
-
Axis Setup and status display
-
Automatically generate initialization
program
-
Multi-program “Windows™” style screen editor
-
Display/Change Inputs, outputs and flags
-
Keypad Emulation
-
Program Debugger
-
Load and save variables/tables to PC
-
Graphical view of table data
-
Online help with MotionPerfect2 and MC basic
-
Configure and initialize distributed I/O
-
Controls to set baud rate, display, ports,
etc.
Because of true preemptive multi-tasking, 3, 7 or 14 processes
can be executed within an MC controller simultaneously,
depending on the model. This enables parts of a complex
application to be developed, tested and run independently, even
though the tasks may be sharing data and motion control
hardware.
The software packages connect using Ethernet,
CTNet, Serial or USB connections. Ethernet communications allow
the drives to be accessed remotely, anywhere in the world.
|
USB |
ETHERNET |
RS485 MODBUS RTU |
CTNET |
MotionPerfect2 |
√ |
√ |
√ |
|
PowerTools Pro |
√ |
√ |
√ |
|
SyPTLite |
√ |
√ |
√ |
|
SyPTPro |
√ |
√ |
√ |
|
Connectivity Software
Control Techniques CTOPCserver allows
easy integration between variable speed drives or power
conversion systems and PC-based software systems such as
SCADA packages.
CTOPCServer
CTOPCServer is an OPC-compliant server
which allows PCs to communicate with Control Techniques drives.
The server supports communication using Ethernet, CTNet,
RS485 and USB. OPC is a standard interface on SCADA packages and is
widely supported within Microsoft® products.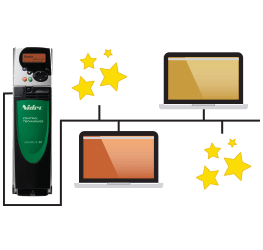
Specifications
CTOPCServer system requirements:
For an industrial application running a modern SCADA
system or a VB application we recommend a major brand name system
certified for Windows NT, 2000 or XP (Windows 9X systems are not
supported) from the office or industrial sectors with the following
specifications:
-
Processor: Any from the AMD Athlon, Athlon XP, Duron
or later, or Intel Pentium III, Pentium 4, Celeron or later running
at 800MHz or greater. For servers running large active namespaces we
recommend Athlon XP or Pentium 4 processors running at 1.8GHz or
greater with 512Mb ram
-
Memory: 256MB RAM
-
Hard drive: 200MB of free hard disk space.
-
Operating system: Microsoft Windows NT4 sp6, Windows
2000 sp4, Windows XP.
-
Microsoft Excel 2000 or later will be required to
make the configuration file. It is not necessary for this program to
be present on the run-time machine
-
Web browser: On OS's prior to Windows XP, Windows
Explorer 5.5 or greater must be installed on the run-time machine as
it provides XML services to the OPC Server. On an NT machine with
IE6, sp1 for IE6 is also required as IE6 installs com components
that are incompatible with server browsing.
Commissioning Software
Control Techniques commissioning software tools help
you get quickly and easily set up a drive.
Control Techniques Connect Software
Based on Control Techniques’ 25 years experience,
Connect software is our latest drive configuration tool
for commissioning, optimizing and monitoring drive/system performance.
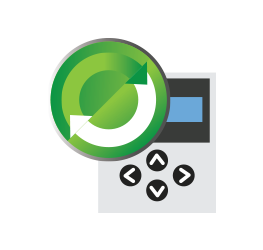
Features of Connect Software
Its development draws from extensive user
research, using human centered design principals to give the ultimate
user experience:
-
Fast task based commissioning and easy maintenance
of the Unidrive
M &
Commander C general purpose drives family is simplified
via familiar Windows interface;
-
Intuitive graphical tools enhance and simplify user
experience;
-
For experienced users, dynamic drive logic diagrams
and enhanced searchable listings are present;
-
Drive and motor performance can be optimized with
minimal specialized drive knowledge;
-
Tool is scalable to match application requirements;
-
Supports the import of Unidrive SP parameter files
and allows full drive cloning (i.e. parameter sets and
application program);
-
Multiple simultaneous comms channels for a more
complete overview of the system;
-
Drive discovery gives the ability to find drives on
a network automatically without the user having to specify their
addresses;
-
Automatic RTU baud rate scanning on the Unidrive M
drives which have a 485 connection.
-
Specifications
System requirements:
Getting Started - Installation
Install Connect on Microsoft Windows (7 or
later) by running the installation program provided. Your
computer will need to have Microsoft .Net 4 installed too - in
the unlikely event it hasn't the installer will download it from
the internet. Note that installation may take some time, but
please be patient.
Installation notes:
-
Any previously installed version of Connect
will be upgraded during the installation. Normally, there is
no need to uninstall the older version.
-
The installation can take quite some time to
complete.
-
Recommended system requirements for
installation:
-
Operating system: Windows 7 with SP1,
Windows 8/8.1 or Windows 10 (32-bit or 64-bit).
-
Disk space: 2GB or more free.
CTSoft Commissioning Software
CTSoft is a drive configuration tool for commissioning, optimizing and
monitoring Control Techniques drives.
CTSoft allows you to:
-
Use configuration wizards to commission your drive
-
Read, save and load drive configuration settings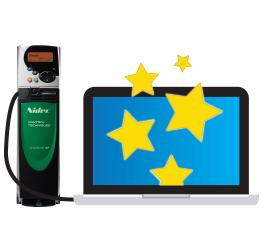
-
Manage the drive’s Smartcard data
-
Visualize and modify the configuration with live
animated diagrams
-
Features
The main features available for CTSoft are:
-
Graphical User Interface
-
Parameter listings for each drive menu
-
Menu block diagrams
-
Terminal configuration
-
Set up wizards
-
Parameter compare (against default and
against file)
-
Various monitoring screens
-
Custom lists for storing frequently used
parameters
-
Parameter files (saving and loading complete
parameter sets)
-
Control panel view for Commander SK drive
with similar functionality to remote keypad
-
Indexer and quick setup tools for
Digitax ST
-
Specifications
CTSoft can be used for configuring the
following Control Techniques drives:
-
Digitax ST Base
-
Digitax ST Indexer
-
Digitax ST Plus
-
Digitax ST EZMotion
-
FXMP25 Field Controller
-
Mentor MP
-
Unidrive 'Classic' in open-loop, closed-loop
vector and servo modes
-
Unidrive SP open-loop, closed-loop vector
servo modes and regen mode
-
Commander SK drives
-
Commander GP20 Drive in open-loop,
closed-loop vector
-
Unidrive ES open-loop, closed-loop vector
and servo modes
-
Unidrive PV
CTSoft system requirements:
-
Pentium IV 1000MHz or better recommended
-
Windows 7, Windows Vista, Windows XP or
Windows 2000 is required.
-
Internet Explorer V5 or later should also be
installed
-
Absolute minimum of 800x600 screen
resolution. 1024x768 is recommended as a minimum.
-
Adobe Acrobat 5.05 or later (for parameter
help)
-
256MB RAM
-
Microsoft .NET Framework Version 2.0
-
Note that you must have administrator rights
to install CTSoft
-
If you have a previous copy of CTSoft
installed you must uninstall it first (you will not lose any
existing projects)
CTScope Software
CTScope is a full-featured software oscilloscope
for viewing and analyzing changing values within the drive.
The time base can be set to give high speed capture for
tuning or for longer term trends. The user interface is based on a
traditional oscilloscope making it familiar and friendly to all
engineers across the globe.
CTScope Features:
-
Four channels
-
Triggers
-
Channels can capture parameter values from different
nodes
-
Scaling & offset per channel
-
Cursors to aid measurement
-
Zoom facility
-
Scroll/Panning facility
-
Save/load scope configurations with or without data
-
Print facility
-
Sample period possible down to 1ms with Turbo CTNet
-
Works with CT-RTU, CTNet, Ethernet (CT-TCP/IP),
MD29MON and ANSI interfaces
-
Specifications
CTScope system requirements:
-
Pentium III 500MHz or better recommended
-
Windows 2000/XP/Vista operating system.
NOTE: Windows 95/98/98SE/ME/NT4 and Windows 2003 Server are
NOT supported
-
Internet Explorer V5 or later should also be
installed
-
Absolute minimum of 800x600 screen
resolution. 1024x768 is recommended as a minimum
-
128MB RAM
Note that you must have administrator rights to
install CTScope. You do not need administrator rights to run
CTScope, but this will be necessary should you wish to
simultaneously run CTSoft or SYPTLite.
CTVue HMI Software
Control Techniques' free CTVue Software
makes it easy to program our broad range of HMI solutions. CTVue is a
straightforward programming and configuration software tool for the
complete line of CTVue HMIs.
Easily create your customized machine interface with
free CTVue configurator software!
-
Features
This free simple-to-use software provides quick
connection and access to all the features available, including
the advanced features such as Data Logger, Web Server and
Security Manager.
From the small CTVue-304K color touch screen to
the large 15” models the CTVue Configurator software
provides the same setup options and convenience of having
pre-mapped drive parameters for all the Control Techniques AC,
DC and Servo drive products.
This feature along with the built in image
library can speed setup and commissioning of complex systems.
CTVue software configurator includes
communication drivers for many of the popular PLC manufacturers
which provides the necessary protocol conversion with minimal
setup required.
|