45 A – 700 A (10 hp – 400 hp)
208 / 230 / 380 / 480 Volts
3Ø DC Package
Control Techniques’ Quantum MP
is a packaged
Mentor MP high performance DC drive providing
reliability, power, and control to increase productivity for
both new machines and applications in which DC
motors are already installed.
The Quantum MP package includes the drive,
fusing, power switching and 115Vac interface making it the
ideal choice for rapid retrofits with regenerative and
non-regenerative modules available to suit your application.
The Quantum MP saves engineering time and
panel space making it ideal for North American customers.
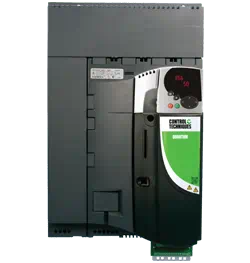
-
Features
Flexible system integration
Quantum MP is a modern packaged DC
drive that has unparalleled flexibility through the
integration of Control Techniques' AC drive control
technology on a DC drive. This means the Quantum MP
inherits system integration flexibility, such as:
-
Two available SM option module
slots for automation control, I/O, feedback
devices and communications
-
SMARTCARD for PLC program and
parameter storage
-
PC tools for easy configuration,
monitoring, and diagnostics
Additional features include:
-
Patented (pending) galvanic
isolation protects control circuits against poor
quality industrial power supplies and high
voltage circuitry
-
Powerful onboard intelligence
fine-tunes the drive’s functionality to the
application and allows the removal of
troublesome analog control circuits
-
Communication options include
EtherNet/IP, Modbus TCP, PROFIBUS DP, and
DeviceNet allowing Quantum MP to be integrated
within any automation system
-
CTSoft, a windows-based software
package, provides an intuitive environment for
configuring the drive's functionality
-
Quantum MP integrates closely
with Control Techniques AC drives using CTNet
drive-to-drive communications
Technology for reliability and performance
Quantum MP takes a step forward in
performance, robustness and reliability:
-
High performance motor control
-
Galvanic isolation (patent
pending) between power and control protects the
control circuits and other equipment connected
to the drive from the high voltages on the power
circuit. This feature is unique on DC drives
-
Protection system against poor
industrial power supplies and lightning strikes
-
Integrated drive and motor
protection
Flexible field control
Internal field controller with
intelligent field weakening means that 90 % of
applications require no additional external
controller
-
Integrated field control on
frame size 1 to 8 A
-
Integrated field control on
frame size 2 to 20 A
-
Flux control for enhanced
open-loop performance
-
External FXMP25 field
control to 25 A
Specifications
-
High-speed semiconductor fusing
for reliable circuit protection
-
115 Vac control interface to
coordinate signals and commands to the drive
-
DC loop contactor (with DB pole
up to 250 hp @ 480 Vac) disconnects the Quantum
MP drive from the motor armature when stop
command is given or in the event of a power
failure
-
DC output fuse on all Regen
models helps avoid nuisance trips
-
Regenerative and
non-regenerative modules available to best match
application needs
-
Multiple fieldbus options
including EtherNet/IP, Modbus TCP, PROFIBUS DP,
and DeviceNet are used to integrate Quantum MP
drives into automation systems
-
Enclosure IP00
Environment
-
Ambient operating temperature:
32 ° to 131 °F (0 ° to 55 °C )
-
Derate current 1.5% per °C from
104 ° to 131 °F (40 ° to 55 °C )
-
Cooling method QMP25-QMP45
natural convection
-
QMP75 and larger forced
convection
-
Humidity 90 % relative humidity
at 122 °F (50 °C)
-
Storage temperature: -40 ° to
131 °F (-40 ° to 55 °C )
-
Altitude: 0 to 9,842 ft (0 to
3,000 m), derate 1 % per 380 ft (100 m) between
3,280 ft (1,000 m) and 9,842 ft ( 3,000 m)
AC supply requirements
-
Supply voltage 208 to 480VAC ±10
%
-
Frequency 48 to 65 Hz
-
Supply fault current 100 kA
-
Drive efficiency 99 %
-
Armature voltage (max.)
non-Regen drives — 1.35 X input VAC; Regen
drives — 1.15 X input VAC
-
Field voltage (max.) 0.9 X input
VAC with 1-phase input
Control
-
Analog input resolution: 16-bit
plus sign, 250 μs (Qty 1), 10-bit plus sign, 250
μs (Qty 2)
-
Speed loop: 250 μs loop update
-
Current loop: 35 μs current
sampling time
-
Feedback methods
-
Encoder (resolution 0.01 %)
-
DC tachometer (resolution 0.1
%); AC tachometer (resolution 1 %) (300 V max.)
-
Armature Voltage (resolution 5 %
)
-
Optional additional incremental
and absolute encoders (Qty 2)
-
Field control current regulated
with flux control
-
QMP25-QMP 8 A
-
QMP350-QMP700 20 A
-
Optional FXMP25 25 A
-
Serial communications: 2- or
4-wire RS422 or RS485, optically-isolated
-
Protocol: ANSI x 3.28-2.54-A4 or
Modbus RTU
-
Baud rate: 300 to 115,200
Protection & diagnostics
-
Control: Galvanic electrical
isolation, 24 Vdc power supply
-
Supply: Loss, under-voltage,
overvoltage, transient suppression,
semiconductor fuses
-
Armature: Open circuit, I2t
overload, instantaneous over current,
semiconductor fuse (Regen only)
-
Field: Loss, over current
-
Motor: Motor over-temp switch or
thermistor over-temperature trips
-
Drive thermal: Heatsink, SCR
junction, control board and option module (s)
-
Current loop loss: Loss of
analog current reference
24 Vdc I/O
-
Digital inputs: 3 x 24 Vdc
-
Digital input/outputs: 3 x 24
Vdc
-
Analog inputs: 1 x 16-bit
differential
-
0-10 V, 2 x 10-bit voltage or mA
-
Analog outputs: 2 x 10 bit
voltage or mA
120 Vac I/O
-
Inputs
-
EMERGENCY STOP
-
STOP
-
RUN
-
JOG
-
FWD/REV
-
RESET
-
Outputs
-
Relays (quantity 2)
Ratings and dimensions

*Current ratings are at 104 °F (40
°C) with 150 % overload for 30 s. (R) indicates
optional order code for 4-quadrant operation.
**These models do not include
dynamic braking contactors.
HP provided for convenience. Always
size drive based on motor Amps.
Applications
Many DC drive applications are for retrofit systems to
improve the performance and prolong the life of existing plants and
machinery. New applications for DC drives include:
-
High Power applications
-
Ski lifts
-
Printing Presses
-
Heavy Moveable Structures
-
Lumber and Paper Milling
-
Dual-turret winding
-
Plastic and Rubber Extrusion
-
Cranes, Hoists, and Cabling
-
Iron, Steel and Glassworks
-
Tilt Vessels, Coilers, Spoolers
-
Metal Fabrication and Wire drawing
-
Winding and unwinding
-
Pulp and Paper processing
-
Metal Rolling and processing
Benefits
-
Powerful onboard intelligence allows the drives
functionality to be finely customized to the application and allows the
removal of troublesome analog control circuits
-
Modular approach to high power drives allows multiple
Quantum MP drives to be connected in parallel or series to economically
achieve the required motor current and voltage rating
-
CTSoft, a windows based software, provides an intuitive
environment for configuring the drives functionality
-
Our knowledge and experience in DC drive systems allows us
to recommend the best solution for your individual circumstances
-
Quantum MP integrates closely with the Control Techniques
AC drives using CTNet, drive-to-drive communications
-
Regenerative and non-regenerative modules available to suit
your application
-
Fieldbus options including; Ethernet, Profibus and
DeviceNet allow Quantum MP to be integrated within an automation system
-
Worldwide expertise and support
In addition to the features of the Mentor MP, the Quantum MP
drive includes:
-
High speed semiconductor fusing
-
115 VAC control interface
-
DC loop contactor (with DB pole up to 250 hp @ 480 VAC)
-
DC output fuse on all Regen models
OPTIONS
A wide range of solution modules are available to allow you to
customize Quantum MP for your application.
-
Keypads and
parameter storage
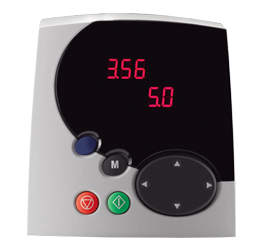
|
MP-Keypad
MP-Keypad is a multi-lingual,
hot-pluggable, backlit LCD display
for Mentor MP drives |
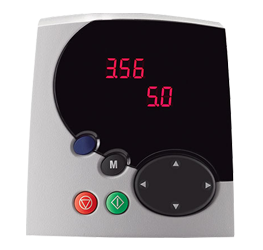
|
SM-Keypad
SM-Keypad is a high brightness
LED keypad for Unidrive SP (except
frame size 0) and Mentor MP drives |
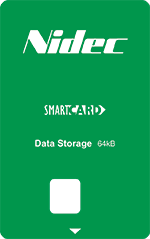
|
Smartcard
This memory device can be used to
backup parameter sets and PLC
programs and copy them from one
drive to another |
Drive Interface
Units - Communications
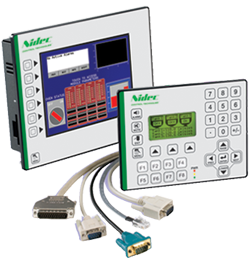
|
Operator
Interfaces and HMI
The powerful CTVue HMI (Human
Machine Interface) line and
integrated drivers for Control
Techniques drives make it easy to
integrate HMI with CT drives |
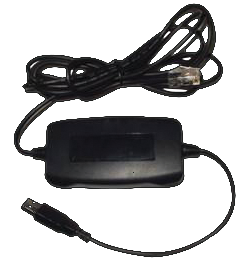
|
CT USB Comms
Cable
The USB Comms cable allows the
drive to connect to a PC for use
with Unidrive M's PC tools* |
-
Automation
and Motion option modules
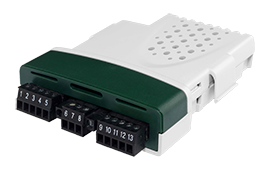
|
SM-Applications Plus
SM-Applications Plus offers
high performance programmable
logic and motion control
together with high speed I/O and
CTNet, a high speed Fieldbus |
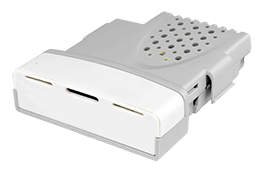
|
SM-Applications Lite V2
User programmable logic and
motion control module for
standalone drive applications or
for when the drive is connected
to a centralized controller via
I/O or Fieldbus |
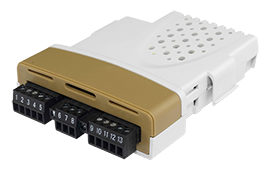
|
SM-Register
A flexible, high performance
solution for programmable motion
requiring high speed
registration features |
Communication option modules
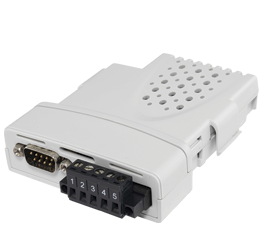
|
SM-CANopen
CANopen interface supports
various profiles including several
drive profiles |
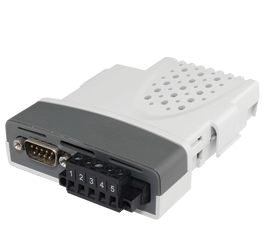
|
SM-DeviceNet
SM-DeviceNET option module |
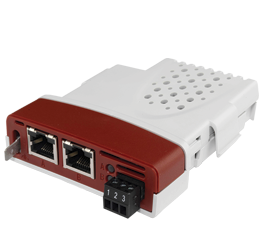
|
SM-EtherCAT
Slave/follower option module, for
high performance servo applications |
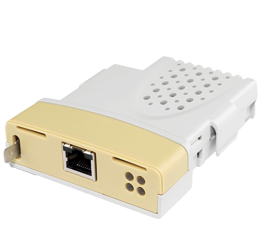
|
SM-Ethernet
supports Ethernet/IP and Modbus
TCP/IP and can generate emails.
Provides high speed drive access,
global connectivity and integration
with IT network technologies |
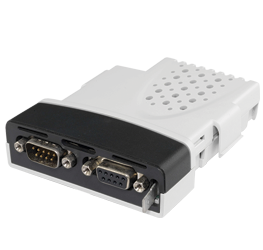
|
SM-Interbus
Interbus interface option module |
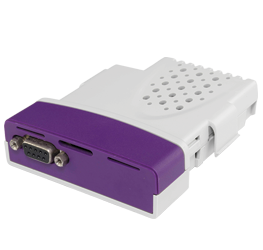
|
SM-PROFIBUS-DP
Slave/follower option module |
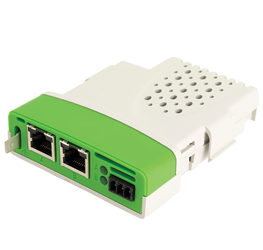
|
SM-PROFINET
PROFINET is an Ethernet based
industrial network protocol adapting
Ethernet hardware and protocols |
Input and
Output Option Modules
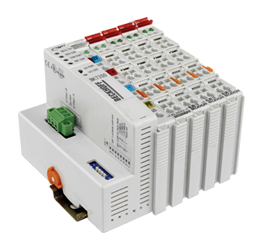
|
CTNet IO
Flexible I/O system for
remote connectivity with Control
Techniques’ SM-Applications Plus
and SM-Register option modules |
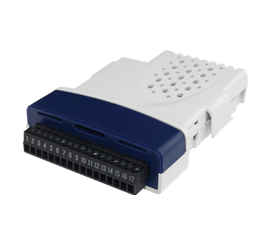
|
SM IO 24V
Protected
Overvoltage protected I/O
module |
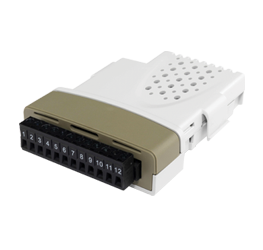
|
SM-IO 120V
Module that provides digital
I/O rated to 120Vac |
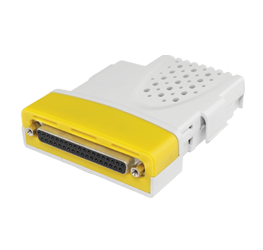
|
SM-IO 32
Extended digital I/O, adding
32 digital high speed
bi-directional I/O points to the
drive |
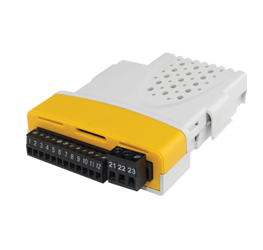
|
SM-IO Lite
Extended I/O interface with
reduced functionality |
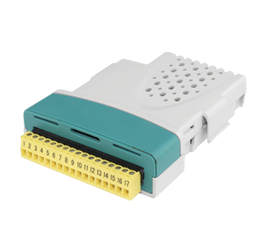 |
SM-IO PELV
NAMUR standard I/O interface
with high speed I/O |
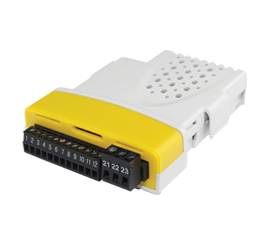
|
SM-IO Plus
Extended I/O interface to
increase the number of I/O
points on a drive |
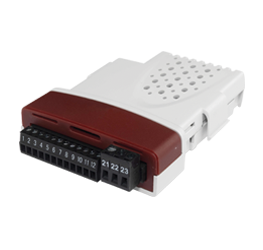
|
SM-IO Timer
Extended I/O option module
with real time clock |
Feedback
Option Modules
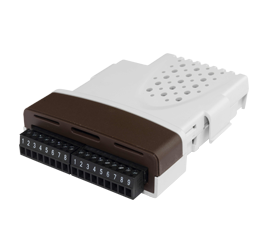
|
SM-Encoder
Output Plus
Incremental encoder input and
output option module that
enables connection with external
motion controllers |
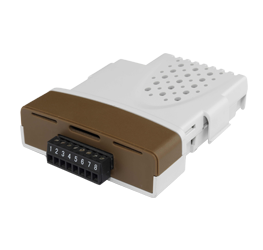
|
SM-Encoder
Plus
Incremental encoder input
option module |
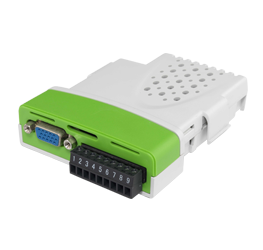
|
SM-Universal
Encoder Plus
Additional combined encoder
input and output interface
supporting Incremental, SinCos,
HIPERFACE, EnDAT and SSI
encoders |
External
Field Control
Field Regulator
Optional FXMP25 external field controller for field
currents up to 25A
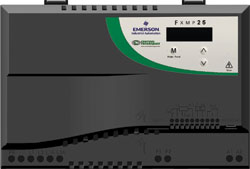
Power Accessories
Remote I/O
CTNet I/O
Flexible I/O system for remote connectivity using Control
Techniques' CTNet Drive-to-drive network

Software
-
Control Techniques Windows-based
software packages connect using Ethernet, CTNet,
Serial or USB connections.
Ethernet communications allow the
drives to be accessed remotely, anywhere in the
world.
Control Techniques' software suite makes it easy to access
the complete feature set of our drives. These tools provide quick
setup of the drive, optimize tuning, configuration back-up, programmable
control and communications link set up.
-
CTSoft - Drive configuration
-
CTScope - Software oscilloscope
-
SyPTLite - Ladder program editor
-
SyPTPro - Full automation system programming tool
-
CTOPCServer - OPC compliant server for interfacing with
Control Techniques' drives
The Software tools communicate using Ethernet, CTNet,
Serial or USB connections. Ethernet allows the software tools to easily
use the internet infrastructure allowing Control Techniques drives to be
accessed remotely, from virtually anywhere around the world.
CTSoft
CTSoft is a configuration tool for commissioning, optimizing
and monitoring Control Techniques drives. It allows you to:
-
Easily configure the drive using wizards
-
Read, save and load drive configuration settings
-
Manage the drive's smartcard data
-
Monitor drive parameters and status
-
Visualize and modify the configuration with live animated
diagrams
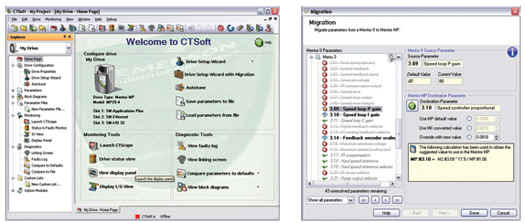
CTSoft is free of charge and can be obtained by clicking the
download tab on this page.
CTScope
CTScope is a full featured software oscilloscope for viewing
and analyzing changing values within the drive. The time base can be
set to give high speed capture for tuning or intermittent capture for longer
term trends. The interface is based on a traditional oscilloscope,
making it familiar to engineers across the globe.
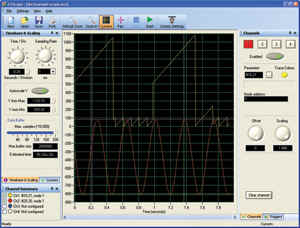
CTScope is free of charge and can be obtained by clicking the
download tab on this page.
SyPTLite
SyPTLite is an easy to use ladder logic program editor,
suitable for simple drive applications. SyPTLite is ideal for controlling
basic logic and sequencing onboard PLC and with SM-Applications Lite V2 solution
module.
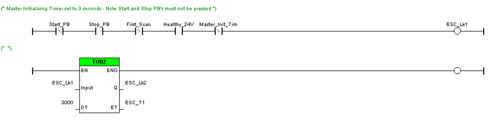
SyPTLite is free of charge and can be obtained by
clicking the download tab on this page.
SyPTPro
SyPTPro is a full featured automation development environment
that can be used for creating solutions to single or multiple drive
applications. The programming environment fully supports three industry
standard programming languages: Function Block, Ladder and Structured Text.
Motion is configured using PLCopen function blocks that support a master and
slave axis configuration.
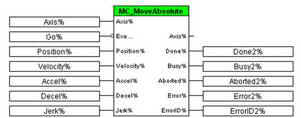
SyPTPro is also used to configure CTNet, a high speed
drive-to-drive network that links together multiple drives, SCADA, operator
panels and I/O to form an intelligent networked system.

CTOPCServer
CTOPCServer is an OPC compliant server that allows PCs to
communicate with Control Techniques' drives. The server supports
communication using Ethernet, CTNet, Serial RS485 and USB. OPC is a
standard interface on SCADA packages and is widely supported within Microsoft
products. The server is supplied free of charge and can be obtained by
clicking the download tab on this page.
Software Available
-
Control Techniques Windows-based
software packages connect using Ethernet, CTNet,
Serial or USB connections.
Ethernet communications allow
the drives to be accessed remotely, anywhere in
the world.
Commissioning and monitoring
software
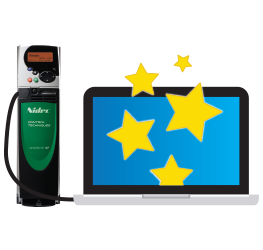
|
CTSoft -
Drive configuration tool for Control
Techniques drives CTSoft
is a drive configuration tool for
commissioning, optimizing and
monitoring Control Techniques drives |
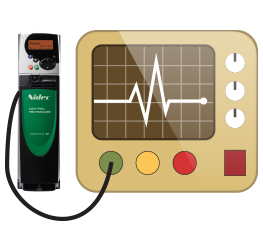
|
CTScope -
Real-time software oscilloscope
CTScope is a real-time full featured
software oscilloscope for viewing
and analyzing changing values within
the drive |
Automation and motion
programming software
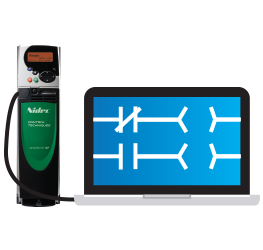
|
SyPTLite - Fast user
program editor for Control
Techniques drives
SYPTLite is a ladder diagram editor
allowing users to develop simple
programs for Control Techniques
drives and option modules |
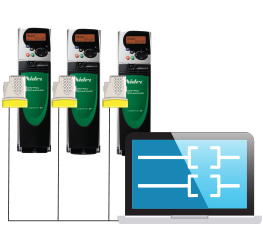
|
SyPTPro - System
programming toolkit for drive
automation systems
SyPTPro provides a full featured
programming environment for PLC and
motion control onboard Control
Techniques AC, DC and servo drives |
Connectivity Software
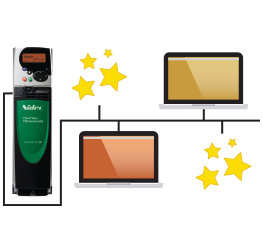
|
CTOPCServer - OPC
compliant server
CTOPCServer is an OPC compliant
server for interfacing your own PC
software with Control Techniques |
HMI Software

|
CTVue HMI
Software Control
Techniques CTVue human interface
software tool enables the operator
to easily configure drive-related
control variables. |
The software packages connect using Ethernet, CTNet,
Serial or USB connections. Ethernet communications allow the drives to be
accessed remotely, anywhere in the world.
|